Чертежи редукторов
В этой категории вы сможете найти чертежи редукторов
различных конструкций, типов и предназначений. Вообще редуктор – это механизм, передающий и преобразующий вращающий момент с одной или более механическими передачами. Основные характеристики редуктора – передаточное отношение – отношение угловой скорости ведущего вала к угловой скорости ведомого, передаваемая мощность и др.
Самым главным параметром редуктора является тип механической передачи. По этому признаку редукторы делятся на:
- цилиндрические
- конические
- червячные
- планетарные
- циклоидальные и т. д.
Количество ступеней редуктора тоже играет не последнюю роль. В промышленности распространены также мотор-редукторы – редукторы, соединенные с электродвигателем. Редуктор, который ступенчато изменяет угловую скорость, называется коробкой передач, а бесступенчатую – вариатором.
Обычно редуктор понижает угловую скорость и повышает вращающий момент, если делается наоборот, то такое устройство называется мультипликатором.
Не секрет, что из всех чертежей чертежи редукторов пользуются, наверное, самой большой популярностью у студентов, очевидно потому что в общетехнической дисциплине «Детали машин» в курсовом проекте приходится разрабатывать именно редуктор. Выбор данного объекта для конструирования не случаен, разработав редуктор «по уму» вы существенно повысите свои навыки и умения в проектировании.
Однако многим такая задача кажется непосильной, особенно вся эта куча чертежей, которую надо нарисовать. На самом деле проектирование редуктора не является таким уж сложным делом, так как методика разработана, как говорится, «от и до», поэтому остается только взять книгу за авторством Дунаева и Леликова «Конструирование узлов и деталей машин» и делать все, как там написано, практически не задумываясь. Никто конечно не отрицает, что все посчитать и сделать все чертежи будет быстро, особенно если делать все правильно и первый раз, а не переделывать курсачи одногруппников или скачанные в Интернете.
Расчеты поддаются довольно неплохой автоматизации, впрочем как и чертежи редуктора, если сильно постараться. При должном желании можно написать программное обеспечение, в котором за одно нажатие кнопки будет сгенерированы и записка и чертежи. Конечно, в бесплатном доступе в Интернете такой софт найти будет тяжело, а если писать самому, то быстрее сделать 5 курсовых вручную. Хотя даже простое применение Маткада существенно автоматизирует данный процесс, ну а чертежи придется, скорее всего, рисовать– или «перебивать» нарисованные кем-то другим.
На нашем сайте вы можете скачать чертежи редукторов различных типов.
Лабораторний практикум. Виконання креслень редуктора до курсового проекту «Деталі машин»
Склав викладач к.т.н. П.С. Носов. по матеріалам Кидрука М.И. КОМПАС-3D V10 на 100%.
Лабораторная работа № 9 Тема: Создание сборочного чертежа одноступенчатого цилиндрического редуктора. Создание зубчатого зацеления колеса и шестерни. Теретическая часть
Для начала несколько слов о том, что мы будем чертить. Редуктор – это машиностроительный механизм, предназначенный для согласования рабочих параметров электродвигателя и рабочего органа машины (насоса, конвейера, лебедки и т. п.). Рабочие параметры – это вращательный момент и частота вращения вала. В редукторе, как правило, идет понижение частоты вращения и, соответственно, повышение величины передаваемого момента (в противном случае это уже будет не редуктор, а мультипликатор). Необходимость согласования параметров возникла из-за того, что асинхронные электродвигатели имеют строго определенную частоту вращения и выдаваемую мощность, а на входном валу рабочего агрегата силовые параметры определяются требованиями пользователей (например, количество воды, подаваемой насосом, задает частоту вращения его вала) или условиями работы агрегата (например, скоростью подъема груза). По этой причине параметры двигателя почти никогда не совпадают с теми, которые необходимы в реальном производстве. Трансформация рабочих параметров осуществляется при помощи механических передач зацепления. В редукторах используются преимущественно зубчатые цилиндрические, зубчатые конические или червячные механические передачи. Возможно комбинирование нескольких передач (одного или разных типов) в одном редукторе, например редуктор цилиндрическо-червячный или коническо-цилиндрический. Если в редукторе идет понижение силовых параметров с применением одной механической передачи, то он называется одноступенчатым (рис. 2.79), если с использованием двух последовательно размещенных передач – двухступенчатым, если трех – трехступенчатым.
Рис. 2.79. Одноступенчатый цилиндрический шевронный редуктор (корпус в разрезе)
Исходные данные
Допустим, нужно спроектировать редуктор исходя из таких данных:
Тип редуктора – цилиндрический одноступенчатый косозубый;
Вращающий момент на рабочем валу машины (на выходном валу редуктора) – 1200 Н·м;
Необходимая частота вращения вала – 15 рад/с;
Режим загруженности агрегата – средний.
Дополнительные данные, которые были учтены во время проектирования (согласно рекомендациям стандартов или другой технической литературы), включают:
Коэффициент полезного действия цилиндрического косозубого зацепления – 0,97;
Передаточное число редуктора u – 3, 55;
Коэффициент ширины зубчатого венца ψ ba – 0,6;
Число зубьев шестерни z ш – 20 шт.;
Угол наклона линии зуба β – 15°;
Материал шестерни – сталь 40, нормализация;
Материал колеса – сталь 50, нормализация.
В результате проектных расчетов были получены такие характеристики проектируемого агрегата:
Вращающий момент на входном (ведущем) валу редуктора – 352 Н·м;
Угловая скорость ведущего вала – 53, 25 рад/с;
Число зубьев колеса z к – 71 шт.;
Стандартный нормальный модуль зубьев m – 5, 5 мм;
Межосевое расстояние передачи a ω – 259 мм;
Делительный диаметр колеса d к – 404 мм;
Делительный диаметр шестерни d ш – 104 мм;
Ширина колеса b к – 155 мм.
Все параметры, вычисленные при проектировании, подтверждены проверочными расчетами.
Результат расчета валов дал следующие значения (рис. 2.80):
Размеры ведущего вала: d 11 = 45 мм,d 12 = 50 мм,d 13 = 55 мм,d 14 = 63 мм иd 15 = 71 мм;
Размеры ведомого вала: d 21 = 71 мм,d 22 = 75 мм,d 23 = 80 мм,d 24 = 85 мм иd 25 = 90 мм.
Рис. 2.80. Схема вала редуктора
В принятых индексах диаметров вала первая цифра означает номер вала (1 – ведущий, 2 – ведомый), а вторая – номер участка вала, что отвечает схеме на рис. 2.80 (1 – участок под шкив или колесо, 2 – переходной участок, 3 – диаметр вала под подшипники, 4 – посадочный участок под колесо или шестерню, 5 – диаметр упорного буртика).
Значения диаметров всех участков обоих валов приведены к стандартному ряду Ra40.
Этих данных достаточно для того, чтобы начать построение. В процессе выполнения чертежа отдельные геометрические и компоновочные характеристики будут уточняться, а затем воплощаться на чертеже.
Сборочный чертеж редуктора выполняют на основании его эскизного проекта. Содержание эскизного проекта редуктора переносят на лист чертежной бумаги формата А1: разрез по плоскости разъема корпуса и крышки редуктора - в том же масштабе, а главный вид и вид сбоку обычно уменьшают. Затем переходят к проектированию корпуса, который является ответственным узлом, так как воспринимает усилия, возникающие в зубчатых передачах, и силы, приложенные к выходным концам валов. Конструкция его должна быть прочной и жесткой, так как его деформации могут вызвать перекос опор, валов и, следовательно, неравномерное распределение нагрузок по длинам зубьев. Корпус редуктора может быть как сварным, так и литым. Толщину стенки литого корпуса, отвечающую требованиям технологии литья и необходимой жесткости, определяют по формуле
где - крутящий момент на тихоходном валу редуктора, Н·м.
Толщину стенок сварного корпуса принимают равной 0,7 толщины стенок литого. На чертеже проводят штриховой линией на расстоянии δ от контура внутренней стенки корпуса след внешней стенки. Плоскости стенок, встречающиеся под прямым и тупым углом, сопрягают дугами радиусами r и R, как показано на рисунке 12, а. Если стенки встречаются под острым углом, рекомендуется их соединять вертикальной стенкой, как на рисунке 12, б. В этих случаях принимают:
, .
Рисунок 12
В отдельных местах корпуса (например, в местах расположения обрабатываемых платиков, приливов, бобышек, во фланцах) толщину стенки увеличивают до δ 1 . Если отношение толщины , то сопряжение стенок производят радиусом , как показано на рисунке 12, в.При одно сечение должно переходить в другое плавно, как на рисунке 12, г, д. При этом принимают , , .
При конструировании корпусных деталей отделяют обрабатываемые поверхности (приливы под подшипники, смотрового люка, сливные пробки, рым-болты) от черных (необрабатываемых) с учетом припуска на обработку. Обрабатываемые места выполняют в виде платиков (выступов) высотой
Корпуса редукторов обычно выполняют разъемными. Они состоят из двух частей: собственно корпуса и крышки. Разъемы чаще всего выполняют в плоскости, параллельной или перпендикулярной основанию корпуса. Реже применяются наклонные разъемы, как менее технологичные. Для крепления крышки к корпусу по их контурам предусматривают специальные фланцы, в которых выполняют отверстия для размещения крепежных болтов. Болты должны равномерно располагаться по фланцам для надежного обжатия и герметизации стыка. Герметичность разъема обеспечивается механической обработкой и смазыванием разъема перед сборкой герметикой, шеллаком, жидким стеклом или суриком. Болты, расположенные у подшипниковых узлов, назначаются больших диаметров.
Толщину верхнего фланца корпуса (для присоединения крышки), а также толщину фланца на крышке определяют по формуле
.
Толщину нижнего фланца корпуса (для крепления редуктора к раме) устанавливают по зависимости
Ширина фланца определяется как сумма толщины δ стенки корпуса и величины, необходимой для размещения болтов и получения наименьшего габарита, обязательного для работы стандартными гаечными ключами. Диаметры и число болтов выбирают по таблице 8 в зависимости от суммарного межосевого расстояния .
Таблица 8
Болт крепления редуктора к раме | Диаметры болтов, стягивающих крышку и корпус | |||||||||
одноступенчатого | двухступенчатого | трехступенчатого | ||||||||
до | d | Кол. | до | d | Кол. | до | d | Кол. | по фланцу | у подшипников |
М14 | MI6 | M20 | ||||||||
MI6 | М20 | М24 | 0,6·d | 0,75·d | ||||||
М20 | М24 | М30 | ||||||||
М30 |
Расстояния от внешних стенок корпуса до осей размещения головок болтов или гаек и от осей до краев фланцев должны соответствовать рисунку 13 и таблице 9.
Рисунок 13
Таблица 9
d | М8 | М10 | М12 | M14 | М16 | М18 | М20 | М22 | М24 | М27 | М30 | М36 |
S | ||||||||||||
Е | ||||||||||||
А min | ||||||||||||
С |
Вычертив фланцы, используя изложенные выше рекомендации, изображают приливы под подшипники на корпусе и на крышке редуктора. Наружные диаметры приливов вычисляют по формуле
,
здесь D - наружный диаметр подшипника.
Для придания необходимой жесткости корпус усиливают ребрами, расположенными чаще всего у приливов под подшипники. Кроме того, ребра увеличивают поверхность охлаждения корпуса, поэтому их следует ориентировать по направлению движения воздуха: при естественном охлаждении ребра располагают вертикально, а при принудительном - горизонтально, так как принудительный поток воздуха обычно направляют горизонтально. Толщину ребер у их основания принимают равной (0,9...1)·δ, а высоту – . Поперечное сечение ребер жесткости выполняют с уклоном, как на рисунке 14.
Рисунок 14
Для подъема и транспортировки крышки корпуса и собранного редуктора применяют проушины, отливая их заодно с крышкой, как показано на рисунке 15На рисунке 15, а и б проушина выполнена в виде ребра с отверстием, а на рисунке в) - в виде сквозного отверстия в корпусе.
Для подъема и транспортировки корпуса предусматривают проушины или крючья, которые отливают заодно с корпусом, как изображено на рисунке 16.
|
|
|
|
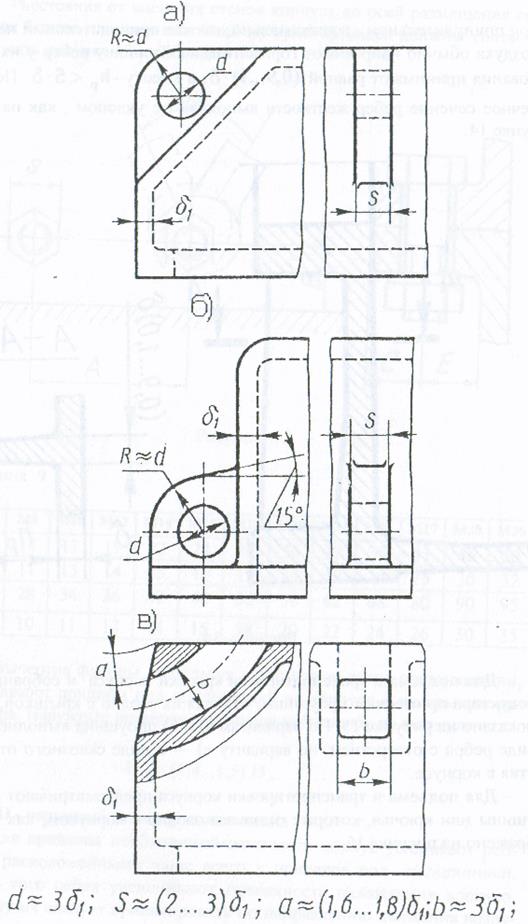
Рисунок 15
Рисунок 16
Чтобы при затяжке болтов (винтов) не происходило смещение крышки относительно корпуса, что может вызвать деформацию подшипников, перед расточкой отверстий под подшипники взаимное положение крышки и корпуса фиксируют двумя коническими штифтами, расположенными во фланцах. Их помещают на возможно большем расстоянии друг от друга. Обработка отверстий под штифты в корпусе производится совместно с крышкой, поэтому все данные для обработки этих отверстий (координаты расположения, количество отверстий, шероховатость поверхностей, размеры) помещают на сборочном чертеже редуктора, как показано на рисунке 17.
Рисунок 17
При работе редуктора масло загрязняется продуктами износа и стареет, поэтому его периодически меняют. Днище корпуса и сливное отверстие должны быть спроектированы так, чтобы не было застойных зон, препятствующих полному сливу масла. С этой целью днище выполняют с уклоном 1-2° в сторону маслоспускного отверстия, а низ отверстия – ниже днища. Для выхода инструмента при обработке отверстия в отливке предусматривают местное углубление. Варианты выполнения сливного отверстия изображены на рисунке 18.
Рисунок 18
Отверстие закрывают пробкой с цилиндрической или конической резьбой, как изображено на рисунке 19.
Рисунок 19
Размеры пробок с цилиндрической резьбой приведены в таблице 10.
Таблица 10
Для создания герметичности соединения под пробку с цилиндрической резьбой ставят уплотняющие прокладки из алюминия или паронита. Для этой цели применяют также кольцо из маслостойкой резины, которое помещают в канавку глубиной t, чтобы оно не выдавливалось пробкой при ее завинчивании. Коническая резьба создает герметичное соединение без дополнительного уплотнения. Поэтому желательно применение пробок с такой резьбой.
Контроль уровня масла производится жезловым, трубчатым или круглым маслоуказателем. Наиболее распространен, ввиду простоты конструкции, жезловый маслоуказатель.
Если крепление жезлового маслоуказателя расположено вблизи масляной ванны, то устанавливают его на резьбе с прокладкой (для предотвращения течи масла), а если далеко - то по посадке Н11/d11. Маслоуказатель устанавливают в специально выполненные на корпусе или крышке редуктора приливы, как показано на рисунке 20.
Рисунок 20
На стержень жезлового маслоуказателя следует нанести риски предельных уровней масла. Так как уровень масла контролируют по его следу на стержне вывернутого маслоуказателя при быстром его вытаскивании, то риски должны быть нанесены (на разрезе при завернутом маслоуказателе) ниже фактического уровня масла на величину длины резьбы.
Жезловой маслоуказатель необходимо применять для цилиндрических редукторов, выполненных по развернутой схеме, а также для червячных с межосевым расстоянием мм. Для червячных редукторов с мм целесообразно использовать трубчатый маслоуказатель. Круглый маслоуказатель рекомендуется для планетарных редукторов, мотор-редукторов и редукторов (коробок скоростей) с принудительной смазкой (контролируют работу масляного насоса).
Для заливки масла в редуктор и контроля правильности зацепления передач в крышке редуктора выполняют смотровой люк прямоугольной или круглой формы с максимально возможными размерами. Люк закрывают крышкой, изготовленной из стального листа или литой из чугуна, алюминия, или прессованной из пластмассы. Под крышку ставят уплотняющие прокладки из технического картона марки А толщиной 1-1,5 мм или резины марки МБ толщиной 2-3 мм.
При работе редуктора (в связи с нагревом масла и воздуха) повышается давление внутри корпуса, что приводит к просачиванию масла через уплотнения и стыки. Чтобы избежать этого, внутреннюю полость корпуса сообщают с внешней средой путем установки отдушины в его верхней точке, чаще всего в крышке смотрового люка. Конструкции отдушин представлены на рисунке 21.
Рисунок 21
Конструкции подшипниковых узлов зависят от типа выбранных подшипников и способа их смазки.
При пластичной смазке подшипники закрывают мазеудержи-вающими шайбами, которые препятствуют вытеканию смазки в полость редуктора и попаданию жидкого масла от смазки зацеплений передач на подшипники. Для этого мазеудерживающие шайбы 1 должны выступать за стенку корпуса или торец стакана (при установке подшипников в стакан), чтобы жидкое масло отбрасывалось центробежной силой, как показано на рисунке 22.
Рисунок 22
При смазке подшипников разбрызгиванием их следует защищать от избытка масла, вытекающего из зубчатого или червячного зацепления, расположенного вблизи подшипникового узла. В этих случаях для ограничения попадания масла в подшипник перед ним на валу устанавливается стальная или пластмассовая маслоотражательная шайба 1. Между этой шайбой и корпусом необходим зазор для небольшого поступления масляного тумана в подшипник. Конструкция такого узла представлена на рисунке 23.
Рисунок 23
Снаружи подшипник закрывают привертными, как на рисунке 23, или закладными, как на рисунке 22, крышками 2. Необходимый осевой зазор в подшипниках обеспечивают установкой набора тонких металлических прокладок 3 под фланцы привертных крышек, а в конструкциях с закладными крышками - установкой компенсаторного кольца 3 при применении шарикоподшипника или нажимною винта при применении конических роликоподшипников.
Для того, чтобы в последствии можно было нанести размеры на рабочие чертежи корпуса и крышки редуктора, нужно на его сборочном чертеже выполнить разрезы по сливной пробке, указателю уровня масла, отдушине, элементам крепления, рым-болту (при его наличии).
Вычерчивают разрезы по крепежным болтам и винтам для определения их размеров, которые заносятся в спецификацию. Следует обращать внимание на определение глубины завинчивания винтов, так как от этого зависят их размеры. Весь крепеж в редукторах применяют с пружинными шайбами.
Раскрывают прямоугольные (конические) контуры зубчатых и червячных колес, полученные еще на стадии эскизного проектирования, то есть конструируют эти детали, используя рекомендации учебных пособий. Следует заметить, что форма зубчатых изделий зависит от типа их производства, простейшие формы имеют колеса, изготавливаемые в единичном и мелкосерийном производствах.
Длину посадочного отверстия колеса (ступицы) принимают не меньше ширины зубчатого венца.
.
Принятую длину ступицы l СТ согласуют с расчетной, полученной при расчете соединения шпоночного, шлицевого или с натягом, выбранного для передачи вращающего момента с колеса на вал, и с диаметром посадочного отверстия d.
Обозначают посадки зубчатых колес на валы. Для обеспечения установки колеса на шейку вала с гарантированным натягом предусматривают на этой шейке конусный или цилиндрический, как на рисунке 24, направляющий участок, выполненный по d11, который будет гарантировать зазор при сборке колеса с валом.
Рисунок 24
Для легкого совмещения шпоночного паза колеса со шпонкой вала граница допуска d11 должна перекрывать центр закругления шпонки.
Редуктор-2D V1.7
Проект Редуктор-2D (рис. 5.22) предназначен для проектного расчета приводов машин, состоящих из двигателя, муфты, передачи гибкой связью и одноступенчатого редуктора, и построения в КОМПАС-График чертежа общего вида редуктора, который входит в рассчитанный привод. Программа позволяет рассчитывать 35 различных схем приводов, которые представляют собой всевозможные комбинации передач гибкой связью (ременной, клиноременной или цепной) с одноступенчатым редуктором (цилиндрическим, коническим или червячным).
Рис. 5.22. Главное окно программы Редуктор-2D V1.7
Проект состоит из двух частей: расчетной – исполняемый файл REDUCTOR.exe и графической, выполненной в виде подключаемой библиотеки к системе КОМПАС, – файл REDUCTOR.rtw.
Примечание
Дистрибутив этого проекта находится на прилагаемом к книге компакт-диске в папке Programs\Редуктор 2D V1.7 (rus). После подключения библиотеки REDUCTOR.rtw к КОМПАС вы можете свободно использовать этот проект в своих целях.
В расчетной части выполняется кинематический и силовой расчет всего привода, проектный расчет выбранной передачи гибкой связью, проектный расчет передачи зацеплением (редуктора), расчет валов и подбор подшипников. Для этого нужно запустить файл REDUCTOR.exe. Сам расчет практически полностью автоматизирован, проектировщик при необходимости может лишь подкорректировать некоторые параметры. Детальное описание, как работать с этой частью проекта, приведено в небольших справках, которые доступны в каждом расчетном разделе. Каждый раздел расчета представлен вкладкой (рис. 5.23): первая вкладка – это кинематический и силовой расчет привода, последняя – расчет валов и подшипников, промежуточные две – расчет механических передач, входящих в привод. Результирующие данные расчетов каждой предыдущей вкладки являются исходными данными для расчетов следующей, из чего следует, что вкладки отображают схему привода.
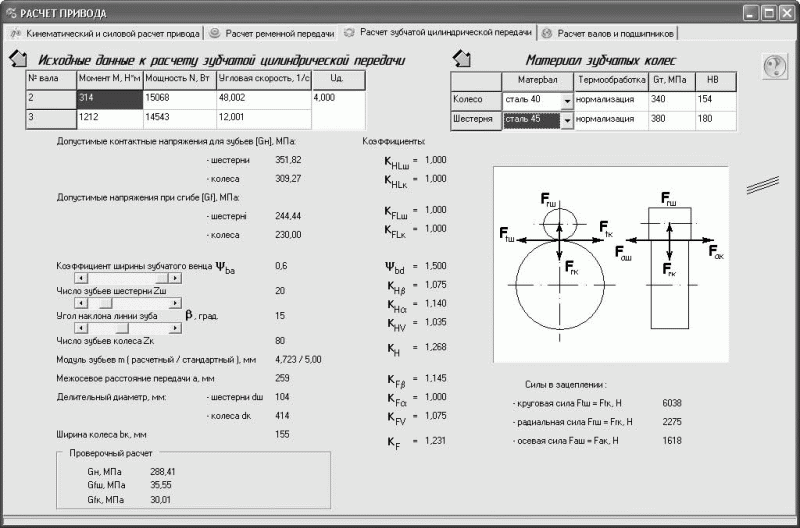
Рис. 5.23. Вкладка, на которой производится расчет цилиндрической зубчатой передачи
После завершения проектного расчета привода можно переходить к графической части проекта (обязательным условием завершения считается выполнение расчета валов, то есть вам необходимо заполнить все вкладки расчетной части). Для этого сначала следует подключить библиотеку REDUCTOR.rtw к КОМПАС. В окне менеджера библиотек выполните команду контекстного меню Добавить описание -> прикладной библиотеки, в открывшемся окне выберите файл библиотеки (REDUCTOR.rtw). В появившемся диалоге Свойства библиотеки вы можете задать имя, которое будет отображено в окне менеджера библиотек, а также выбрать режим открытия (запуска) библиотеки. После подключения библиотека появится в окне менеджера и будет готова к работе.
Примечание
Для данной прикладной библиотеки размещение самого файла REDUCTOR.rtw не имеет значения.
После запуска библиотеки, если окно расчетной части проекта (REDUCTOR.exe) не было закрыто, в окно графической библиотеки будет автоматически загружен редуктор, который был только что спроектирован в расчетной части (рис. 5.24). В противном случае вам придется или заново произвести расчет всего привода, или загрузить данные о рассчитанном приводе, если они, конечно, были сохранены из расчетной части.
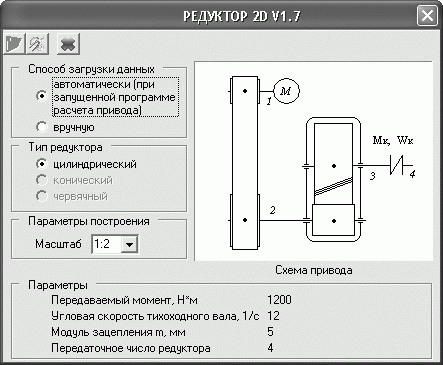
Рис. 5.24. Окно графической части проекта Редуктор-2D V1.7
Все, что остается для построения чертежа редуктора, входящего в привод, – нажать кнопку Чертить лист. Программа самостоятельно создаст лист формата А1 и разместит на нем три проекционных вида редуктора со всеми необходимыми сечениями и размерами.
Пример чертежа редуктора, построенного с помощью этой библиотеки, изображен на рис. 5.25. Кроме цилиндрического косозубого редуктора, в привод входит ременная передача. Привод рассчитывался для следующих исходных данных: вращающий момент выходного вала – 1200 Н · м, угловая скорость – 12 с -1 , режим работы – средний.
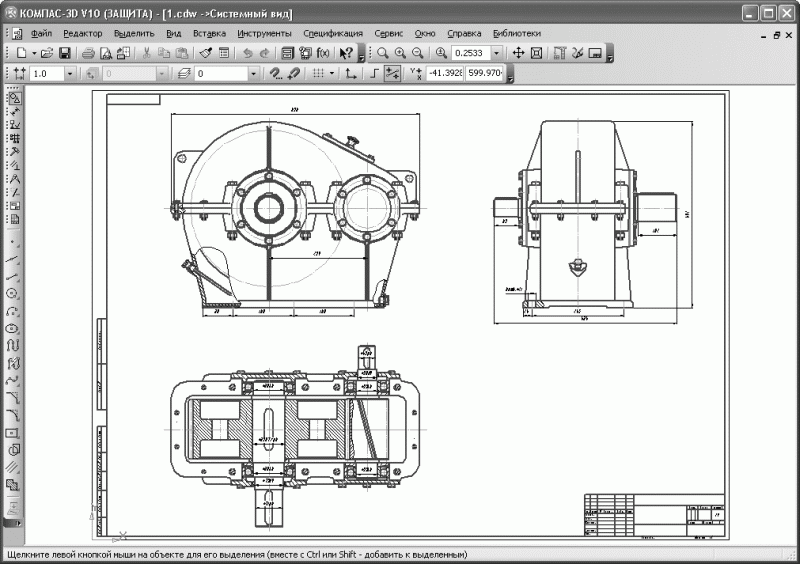
Рис. 5.25. Чертеж цилиндрического редуктора, сгенерированный прикладной библиотекой Редуктор-2D V1.7
Чертежи редукторов двух других типов приведены ниже. Конический редуктор (рис. 5.26) составляет привод вместе с клиноременной передачей и был рассчитан для следующих параметров: вращающий момент – 700 Н · м, угловая скорость – 15 с -1 , режим работы – средний.
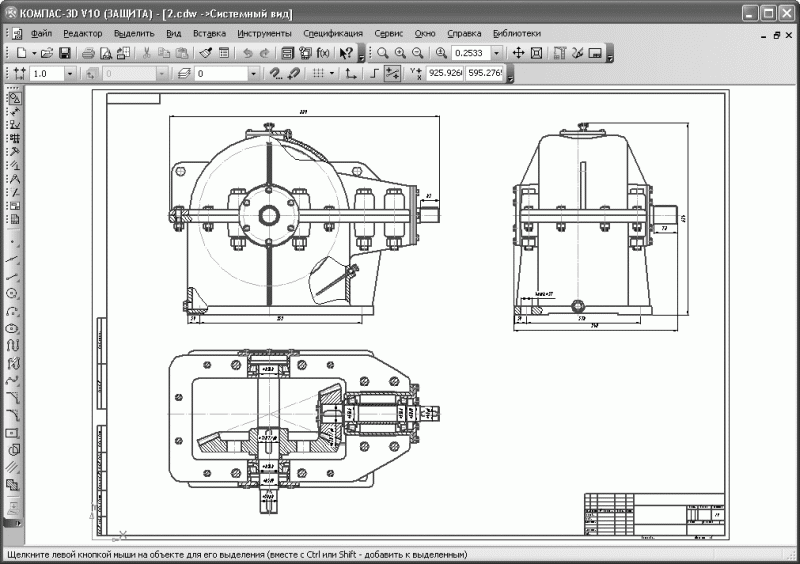
Рис. 5.26. Редуктор конический одноступенчатый
Червячный редуктор, также созданный при помощи этой библиотеки (рис. 5.27), рассчитывался в приводе совместно с цепной передачей для таких параметров: вращающий момент – 2000 Н · м, угловая скорость – 3 с -1 , режим работы – тяжелый.
Похожие статьи