Специально для портала «Перспективы»
Владимир Кондратьев, Сергей Афанасьев
Кондратьев Владимир Борисович – профессор, доктор экономических наук, руководитель Центра промышленных и инвестиционных исследований ИМЭМО РАН. Афанасьев Сергей Андреевич ‒ аспирант ИМЭМО РАН.
Новый этап в развитии российского автопрома начался в 2010 г., когда было принято решение стимулировать выпуск на своей территории автокомпонентов с высокой добавленной стоимостью на основе требований к расширению мощностей иностранных компаний и развитию исследовательских центров. В 2012 г. доля произведенных международными корпорациями на территории России автомобилей впервые превысила долю как импортных, так и отечественных брендов.
Тенденции развития
До 1991 г. Россия уже обладала достаточно развитой автомобильной промышленностью. В 1990 г. в стране было произведено 2 млн автомобилей, из которых 1,2 млн - легковых (700 тыс. выпустил АвтоВАЗ, 200 тыс. ‒ АЗЛК «Москвич», 200 тыс. ‒ Ижмаш, 100 тыс. - ГАЗ «Волга»). По этому показателю СССР занимал пятое место в мире после Японии, США, ФРГ и Франции; по производству грузовиков - третье место в мире, а по производству автобусов - первое. По сравнению с развивающимися странами СССР был абсолютным лидером в автомобилестроении (табл. 1).
Таблица 1. Производство автомобилей в СССР, России и ряде развивающихся стран (тыс. шт.)
Источник: OICA statistics.
В 1990 г. объемы производства автомобилей в СССР были в 1,5 раза выше, чем в Южной Корее, в 2,2 раза - чем в Бразилии, в 4 раза ‒ чем в Китае, в 5,6 раза ‒ чем в Индии и в 6,7 раза ‒ чем в Таиланде. К 2013 г. Россия уже отставала от всех этих стран, включая Таиланд.
При анализе развития российской автомобильной промышленности после 1991 г. можно выделить три основных периода.
Первый охватывает 1991‒2005 гг. Это период быстрого открытия внутреннего рынка, стремительного роста импорта новых и, особенно, подержанных автомобилей. В эти годы начинается «отверточная», или крупноузловая сборка иностранных марок на территории России, позволяющая на льготных условиях ввозить основные компоненты и являющаяся, по сути, формой скрытого импорта.
Второй период (2005‒2010 гг.) знаменует собой переход к так называемому режиму промышленной сборки и строительству первых сборочных заводов полного цикла, с акцентом на локализацию производства (на основе Постановления правительства РФ № 166).
Наконец, третий период начинается в 2010 г., когда государство приняло решение усилить процесс локализации производства и стимулировать выпуск на собственной территории автокомпонентов с высокой добавленной стоимостью на основе требований к расширению мощностей иностранных компаний и развитию исследовательских центров.
На первом этапе, в начале 1990-х гг., происходило снижение производства автомобилей, упавшего в 1994 г. относительно 1990 г. почти на 30%. Некоторый восстановительный рост начался в 1995 г. Это происходило при заметном усилении государственной поддержки отечественного автомобилестроения, которая позволила в 2004 г. выйти на уровень дореформенного 1990 г. В этот период на развитие автомобильной промышленности огромное влияние оказывал импорт иномарок (подержанных и новых). В 2002-2004 гг. в Россию ввозилось свыше 550 тыс. иномарок в год. Если в 2001 г. они составляли 42% от произведенных в стране, то в 2004 г. - уже 61%. Объемы производства отечественных марок продолжали постепенно сокращаться и к 2005 г. снизились на 11% к уровню 2001 г. Доля же иномарок российской сборки, хотя она и увеличилась, составляла всего 14% от общих объемов производства легковых автомобилей в стране (табл. 2).
Таблица 2. Структура производства легковых автомобилей в России в 2001‒2005 гг., тыс. штук
Источники: Росстат агентство, АСМ-Холдинг.
К 2005 г. стало очевидным, что никакой государственной поддержкой не удается реанимировать отрасль в прежней конфигурации. В то же время иностранные компании проявляли все больший интерес к организации производства в России, привлекаемые емким рынком.
На втором этапе (в 2005 г.) государство, используя растущий потребительский спрос и интерес иностранных производителей, приняло решение создать качественно новую отрасль ‒ новые мощности по производству автомобилей, способных конкурировать с импортными. Политика защиты отечественных автомобилей на российском рынке сменилась режимом максимальной открытости для иностранных автомобильных концернов, стремлением сделать отрасль привлекательной для них.
Еще в 1996 г. был построен завод «Автотор», где собирались (а не производились) 27 моделей различных марок, преимущественно компании «General Motors». Однако положительное воздействие на прирост производства отрасли и ВВП оказалось незначительным вследствие потерь бюджета из-за сниженных таможенных пошлин. Довольно скоро правительство обеспокоилось ростом объема крупноузловой SKD-сборки и расширило список простых сборочных операций, которые необходимо осуществлять иностранным компаниям на территории России .
В 2005 г. был принят новый пакет законодательных документов, которым вводился режим промышленной сборки для автомобилей. Его условия содержали обязательства для автопроизводителей осуществлять некоторые производственные операции на российских заводах: сварку кузова и его окраску, сборку двигателей, сборку задней и передней подвески и др. Устанавливалось требование достижения уровня локализации в 30% в течение 7‒8 лет. Режим промышленной сборки изначально был задуман правительством как комплексное решение создания новых или модернизации существовавших мощностей и как альтернатива ввозу готовых иномарок.
Существующим предприятиям давалось 1,5 года для организации на них сварки, окраски и сборки кузова, а вновь создаваемым - 2,5 года. После этого в течение 3,5 лет предприятия обязаны были сократить ввоз автокомпонентов на 30%, а резиденты особой экономической зоны ‒ на 50%.
В 2006-2007 гг. важнейшим качественным изменением отрасли стало создание новых производств по выпуску иномарок. Начали строительство или подписали инвестиционные соглашения крупнейшие иностранные автоконцерны: «Volkswagen», «PSA Peugeot Citroen», «Volvo», «General Motors», «Toyota», «Nissan», «Suzuki», «Hyundai». Они строили автозаводы в основном в Центральном и Северо-Западном федеральных округах. Третьим крупнейшим центром автомобилестроения в России традиционно оставался Приволжский федеральный округ, где уже имелась мощная производственная база. Поэтому там не строили новые заводы, а перепрофилировали действовавшие.
Быстро растущий выпуск иномарок существенно изменил структуру российского рынка легковых автомобилей . В 2001 и 2002 г. реализация иномарок, собранных на российских заводах, была минимальной - 5 тыс. и 10 тыс. штук, в предреформенные 2004 и 2005 г. - уже 130 тыс. и 150 тыс., а в 2008 г. - около 600 тыс. штук. В то же время стремительно увеличивался импорт новых иномарок. Если в 2001 г. в Россию их было ввезено всего около 74 тыс., то в 2007 г. - более 1,2 млн и даже в кризисном 2008 г. - почти 1,5 млн. Всего же в 2002-2008 гг. импорт новых иномарок увеличился в 20 раз. Значительным сегментом рынка оставались импортные подержанные автомобили. Структура рынка в этот период представлена в табл. 3.
Таблица 3. Структура российского автомобильного рынка в 2001-2008 гг., %
| ||||||||
Российские марки | ||||||||
Иномарки российской сборки | ||||||||
Иномарки импортные новые | ||||||||
Иномарки подержанные |
За время реформирования российские марки существенно потеряли свою долю рынка. В 2001 г. на них приходилось 68% рынка, в 2005 г. - 45%, в 2008 г. ‒ только 20%. Несмотря на растущий выпуск иномарок в России, динамика рынка все больше определялась импортом. Если в 2001 г. на ввезенные иномарки (включая подержанные) приходилось 32% всех продаж, в 2005 г. - 46%, то в 2008 г. - уже 62%. Медленно сокращалась доля подержанных иномарок: 2001 г. - 26%, 2005 г. - 20%, 2008 г. - 16%. Наиболее сильно на состояние рынка влиял импорт новых иномарок. Если в 2001-2002 гг. ввезенные новые иномарки составляли 6-7% рынка, то в 2005 г. - 26%, а в 2008 г. - уже 46%, тогда как собранные в России - 1%, 9% и 18% соответственно. Опережающий рост импорта новых иномарок обеспечивался низкими таможенными барьерами. Это была сугубо российская специфика реформирования национального автопрома.
Таким образом, принятых нормативных актов оказалось недостаточно для формирования сбалансированной автомобильной индустрии, выпускающей необходимое количество качественных и современных автомобилей разных ценовых категорий. Российский рынок оказался слишком открыт для импорта иномарок, а условия для организации сборочных производств, предусматривающих ввоз автокомпонентов при уплате минимальных пошлин, были исключительно щадящие. Минимальный объем выпуска, позволявший иностранному концерну беспошлинно ввозить львиную долю компонентов для промышленной сборки, составлял 25 тыс. автомобилей в год.
Учитывая емкость нашего рынка и объемы выпуска крупных иностранных концернов, льготные нормативные условия слабо стимулировали их к созданию полноценных производств.
Процесс локализации столкнулся с рядом негативных факторов. Это, во-первых, небольшие размеры мощностей, разбросанные на достаточно большом расстоянии друг от друга и предназначенные для производства широкого диапазона платформ и моделей, что затрудняло производителям комплектующих осуществление инвестиций. Во-вторых -недостаток качественных базовых материалов (стальной продукции, пластиков и др.), а также поставщиков второго и третьего уровней. Наконец, высокие операционные издержки (по сравнению со странами Центральной и Восточной Европы, куда уже переместили свои мощности многие глобальные поставщики).
В этих условиях в 2010 г. Министерство промышленности и торговли приняло Стратегию развития российской автомобильной промышленности на период до 2020 г., установив цели и определив параметры промышленной сборки, направленные на ускорение процесса локализации. Производители, заинтересованные в продолжении практики пользования пониженными таможенными ставками, должны были взять на себя обязательства по резкому увеличению производственных мощностей, ускорению процесса локализации и интенсификации исследований и разработок на территории России (табл. 4).
Таблица 4. Изменение условий режима промышленной сборки в России
Одним из новых параметров было требование по повышению уровня локализации производства к 2020 г. до 60%. Кроме того, модифицированная версия режима промышленной сборки включала в себя требование к иностранным производителям построить новые или модернизировать существующие мощности, доведя выпуск до 300‒350 тыс. автомобилей в год в течение 36‒48 месяцев после вступления в действие нового соглашения. Среди других требований следует отметить обязательства по организации производства двигателей и трансмиссий полного цикла (без указания конкретных объемов производства) с тем, чтобы 30% производимых в России автомобилей оборудовались произведенными в стране двигателями через 36‒48 месяцев после вступления в силу новых соглашений.
Совершенствование Постановления № 166 создало благоприятные предпосылки для формирования последующих альянсов и серьезных и значительных инвестиций глобальных автомобильных компаний. Было заключено около 400 меморандумов о намерениях. Некоторые из них превратились в инвестиционные соглашения.
Принятые в связи с присоединением России к ВТО регулятивные изменения создают проблемы для автомобильных компаний, локализовавших свое производство на территории страны. Наиболее важным фактором для всех участников автомобильного рынка является снижение импортных пошлин на подержанные автомобили (с 35 до 25%). Согласно данным Министерства промышленности и торговли, объемы импорта подержанных автомобилей в Россию уже достигают 800 тыс. единиц в год, что составляет 30% всего российского автомобильного рынка.
Снижение импортных пошлин может сделать местное производство в режиме промышленной сборки менее привлекательным. Российское правительство, осознавая эту угрозу, разработала новый механизм утилизационного сбора, который направлен не только на создание системы управления жизненным циклом автомобиля, но и на ограничение притока подержанных автомобилей (легковых, коммерческих и автобусов) на российский рынок.
Другой важной проблемой для иностранных автомобильных компаний, организовавших свое производство в России, является регулирование движения товаров в рамках СНГ, что приобретает особую актуальность в условиях дальнейшей интеграции и недавнего Соглашения о зоне свободной торговли. С учетом того, что некоторые страны СНГ имеют большие объемы крупноузловой сборки автомобилей на своей территории, для участников режима промышленной сборки в России могут возникнуть значительные риски в случае снижения или ликвидации таможенных пошлин на импорт из этих стран.
Наконец, следует упомянуть о так называемой Калининградской специальной экономической зоне, которая обладает беспрецедентными таможенными и налоговыми льготами. Чтобы стать резидентом этой зоны, достаточно выполнить минимальные условия. Статус резидента позволяет компании организовать здесь массовую крупноузловую сборку автомобилей без соответствующих обязательств по локализации производства и автокомпонентов (в 2011 г. в этой зоне таким образом было произведено 220 тыс. автомобилей). Такая ситуация не только создает условия для несправедливой конкуренции и демотивирует дальнейшие инвестиции в российскую автомобильную промышленность, но и противоречит долгосрочным планам российской промышленной политики.
Отрасль по производству автомобильных компонентов имеет важнейшее значение для развития всей автомобильной промышленности. По некоторым оценкам, до 60% стоимости автомобиля приходится на поставки комплектующих первого уровня. Очень часто производители автомобильных компонентов берут на себя всю ответственность за проектирование и эффективность функционирования каждого компонента. Они получают функциональные и пространственные спецификации от сборочных автомобильных компаний и осуществляют весь процесс проектирования и производства (от выбора материалов до создания прототипа компонента), обеспечивая автомобильную компанию готовым решением.
Сегодня компании, производящие автомобильные компоненты, являются лидерами в области инноваций. Большая часть современных технологических решений по увеличению безопасности и комфорта в современных автомобилях была разработана такими известными корпорациями, как «Bosch», «Valeo» и др.
Исторически автокомпонентный бизнес развивался двумя путями. Некоторые крупные производители автомобильных компонентов первоначально входили в состав автомобильных компаний (например, «Visteon» была в составе «Ford Motor», «Delphi» ‒ в составе «General Motors», «Denso» - в составе «Toyota» и т.д.). Позже они частично или полностью выделились в самостоятельные компании. Однако возникали и независимые частные компании, как правило, небольшого размера, которые росли вслед за рынком и ростом спроса на новые компоненты.
В России автокомпонентные заводы были построены вместе с автомобильными предприятиями. С одной стороны, это имело ряд преимуществ. Местоположение производства выбиралось таким образом, чтобы минимизировать логистические издержки. Расчет планируемых и вводимых мощностей привязывался к реальным потребностям автомобильных компаний, которые гарантировали рынок сбыта для производимой продукции. С другой стороны, размеры таких автокомпонентных заводов (на которых в ряде случаев трудилось до нескольких тысяч человек) превращали их в негибкие, медлительные производственные структуры. Гарантированный рынок не стимулировал инновации. Отсутствие конкуренции и огромные размеры этих заводов делали их неэффективными в смысле издержек производства. Близость к автомобильным предприятиям не исключала дублирования функций: одни и те же компоненты разрабатывались как инженерными отделами самих автомобильных заводов, так и предприятиями-поставщиками комплектующих. Аналогичная ситуация возникала и с выбором необходимых материалов, лабораторным тестированием и многим другим.
Типичное автокомпонентное предприятие производило широкую номенклатуру продукции. Например, Димитровградский автоагрегатный завод (ДААЗ) выпускал почти все автомобильные изделия: от дверных замков до радиаторов, карбюраторов и осветительной техники. Этот завод был создан в 1967 г. для обеспечения комплектующими Волжского автомобильного завода. Сегодня в ОАО «ДААЗ» входит восемь дочерних самостоятельных предприятий . Общая площадь производственных помещений составляет 316 тыс. м². Для выпуска продукции завод использует 480 наименований комплектующих изделий, более 960 наименований материалов, которые поставляются 180 предприятиями. На заводе занято 8 тыс. человек.
Поскольку новые менеджеры бывших государственных автокомпонентных заводов долгое время продолжали бороться со снижением спроса, ценовым давлением со стороны автомобильных компаний и нехваткой наличности из-за высокой долговой нагрузки, переоборудование предприятий и технологическое обновление не являлись приоритетами. В результате АвтоВАЗ и другие российские автомобильные компании начали многие компоненты импортировать из-за рубежа.
Пришедшие в Россию глобальные автомобильные компании предпочитали работать со своими традиционными поставщиками, стараясь убедить их начать производство автомобильных компонентов на территории страны. В настоящее время такие международные компании, как «Automotive Lighting», «Johnson Controls», «Magna», «Lear», «Valeo», «Delphi» и многие другие объявили о строительстве собственных производственных мощностей в России. Однако объемы локального производства, как и уровень локализации, пока незначительны.
Причина заключается в том, что международные поставщики первого уровня работают с небольшим числом сборочных иностранных автомобильных компаний. Объем заказов, поступающих от одной такой зарубежной компании, недостаточен для оправдания полномасштабного производства автомобильных компонентов с глубокой локализацией. В результате многие компоненты и узлы продолжают импортироваться.
Российские поставщики автомобильных компонентов делятся, в соответствии с мировой классификацией, по типу поставляемой продукции:
- поставщики нулевого уровня - производство компонентов самими производителями автомобилей. Эта практика была традиционной в прежнем автопроме. Сейчас на заводах, производящих российские марки (АвтоВАЗ, ГАЗ, УАЗ, КамАЗ и др.), доля внутреннего производства комплектующих превышает 50% общей номенклатуры;
- поставщики первого уровня - производство готовых систем и модулей для финальной сборки (двигатели, КПП, сиденья, различные системы);
- поставщики второго уровня - поставка компонентов поставщикам первого уровня (поршневая группа для двигателя, рамы сиденья и др.);
- поставщики третьего уровня - производство простых деталей и заготовок для поставщиков второго уровня (литье, болты, различные материалы).
Производитель автокомпонентов может объединять у себя 2-3 уровня. Сейчас в России насчитывается примерно 2 тыс. поставщиков автомобильных компонентов, из них 75% поставляют комплектующие изделия, а 25% - сырье и материалы.
В 2007 г. объем первичного рынка автокомпонентов составлял 7-8 млрд долл. Внешние предприятия производили компоненты на 3,6-4,2 млрд долл., остальное - сами автомобильные заводы. При этом 90% комплектующих были предназначены для традиционных российских автозаводов и только 10% - для сборочных предприятий иностранных компаний.
Масштабы производства российских предприятий, выпускающих автокомпоненты, не соответствуют растущим потребностям российских и совместных автозаводов, а ограниченные финансовые возможности не позволяют провести необходимую модернизацию. Типичны устаревшие технологии и оборудование, низкое качество продукции. Редко у кого есть собственные ноу-хау для разработки и производства современной сложной продукции. Работать на мировом уровне способны не более 5% производителей. Так, за последние 20 лет многие поставщики АвтоВАЗа вообще не осуществляли инвестиций в обновление и ремонт оборудования.
Назовем две стратегии развития российских компаний по производству автомобильных компонентов, которые могут быть успешными. Одна состоит в формировании партнерства с международными автокомпонентными компаниями, заинтересованными в совместной работе на рынке на основе реконструкции и реструктуризации уже существующих мощностей. Этот вариант подходит скорее крупным, достаточно эффективным российским предприятиям, нуждающимся в технологическом обновлении и качественном совершенствовании производства и продуктов.
Вторая стратегия заключается в акценте на самостоятельном развитии с использованием опыта и поддержки родственных компаний. Это касается, в частности, узлов из пластика, когда производитель таких компонентов может использовать опыт и технологии поставщика соответствующих материалов (пластмасс). Помощь производителей базовых материалов, инжиниринговых компаний или проектировщиков оборудования даст возможность выпускать и предлагать на рынке эффективные и качественные компоненты для автомобильных компаний.
К настоящему времени из 25 ведущих глобальных компаний-поставщиков комплектующих в России присутствуют только 13. Тем не менее многие поставщики включают в свои планы растущий российский рынок. В среднесрочной перспективе иностранные автомобильные компании могут довести выпуск автомобилей в стране до 3 млн единиц в год. Кроме того, значительный уже имеющийся парк автомобилей создает потенциальный спрос на комплектующие и запасные части.
Можно отметить несколько производственных ниш, где процесс локализации уже начался или имеет хорошие перспективы. Это металлическое литье, штамповка, внутренние и внешние изделия из пластика (панели, бамперы и т.п.), аккумуляторные батареи, шины и колеса, автомобильное стекло и зеркала, лакокрасочные изделия, электропроводка. Однако до сих пор существуют серьезные проблемы с локализацией производства силовых систем и установок (двигатели, трансмиссии, карданные валы, дифференциалы и др.), шасси, ведущих мостов, подвесок, электроники, систем вентиляции и кондиционирования воздуха.
Чтобы превратить сектор производства комплектующих в конкурентную и устойчивую отрасль, необходимы также более настойчивые усилия по стимулированию научных исследований и разработок. Россия известна своими квалифицированными инженерными кадрами и специалистами в информационных технологиях. Нужно использовать позитивный опыт, накопленный в других сферах экономики ‒ таких как оборонная и авиакосмическая промышленность.
Проблемы повышения конкурентоспособности
Опыт последних лет показал, что формирование конкурентоспособной автомобильной промышленности почти невозможно без использования иностранных технологий и капитала. Оно также предполагает защиту существующих инвестиционных преференций. Эти вопросы играли существенную роль во время переговоров об условиях присоединения России к ВТО.
На этих переговорах Европейский Союз выдвигал требования о сокращении периода активного действия инвестиционных соглашений, снижении уровня локализации, установлении единых ставок тарифов на импорт компонентов и узлов для всех автопроизводителей. В результате Россия согласилась сократить срок действия льгот, а также принять на себя обязательства по выплате компенсаций за возникающие различия в таможенных тарифах из своего бюджета . С целью гармонизации российского законодательства о промышленной сборке с положениями ВТО был установлен переходный период до 1 июля 2018 г., в течение которого уже заключенные инвестиционные соглашения с иностранными инвесторами оставались в силе.
Россия также взяла на себя обязательство снизить таможенные пошлины на импорт новых автомобилей с 25% до 15%. Этого уровня страна должна достичь к концу семилетнего переходного периода, установленного для целой группы товаров. Наиболее существенное снижение тарифов предполагается в течение последних трех лет переходного периода. Кроме того, Россия согласилась компенсировать европейским производителям автомобильных компонентов возможное сокращение импорта, которое может возникнуть вследствие поддержания высокого уровня локализации в режиме промышленной сборки.
Все эти требования, как ожидается, не приведут к резким изменениям в среднесрочной перспективе. Однако по истечении переходного периода уровень защитных тарифов для автопроизводителей в России резко снизится. До этого времени необходимо сформировать стабильную автомобильную промышленность, способную конкурировать с иностранными компаниями на мировых рынках.
Удельный вес российских брендов в структуре рынка продаж легковых автомобилей снизился с 34% в 2010 г. до 25% в 2011 г. и до 21% в 2012 г. Одновременно доля иностранных брендов, произведенных на территории страны, выросла с 34% в 2010 г. до 45% в 2012 г. Возросла также и доля импорта: с 32% в 2010 г. до 34% в 2012 г. (табл. 5).
Таблица 5. Структура рынка продаж легковых автомобилей в России, %
|
2010 г. |
2011 г. |
2012 г. |
Российские бренды | |||
Произведенные в России иностранные бренды | |||
Рис. 1 дает представление о том, как изменялась структура производства иностранных и российских брендов в последние годы.
Рис. 1. Структура производства иностранных и российских брендов в России
Источник: АСМ Холдинг.
Сегодня производителей автомобилей в России можно разделить на три основных типа:
- традиционные российские производители (АвтоВАЗ, ГАЗ, КамАЗ, ЗИЛ и др.). Для них характерны изношенная производственно-технологическая база, ограниченность источников инвестиций, недостаточность масштабов выпускаемых автомобильных платформ и моделей, нехватка современных технологий, гибкости производства и профессионального менеджмента;
- российские сборочные предприятия («Иж-Авто», ТагАЗ, предприятия группы «Соллерс» и др., осуществляющие сборку иностранных брендов). Характеризуются относительно современными технологиями и гибкостью производства, западным стилем управления, неразвитостью собственного инжиниринга и недостаточными масштабами производства для увеличения локализации. Важная проблема - отсутствие у многих из них прав на интеллектуальную собственность (например, «Автотор» является лишь контрактным сборщиком автомобилей);
- иностранные автопроизводители («Ford», «General Motors», «Renault» и т.д.). У них еще малые масштабы производства в России и низкий уровень локализации, отсутствуют, как правило, инжиниринговые центры.
На российском рынке легковых автомобилей представлены многочисленные модели. Это говорит о его относительной развитости, но создает проблемы конкурентоспособности по масштабам производства. Производственные мощности АвтоВАЗа, который остается основным традиционным производителем легковых автомобилей, достигают 1 млн единиц в год. Большинство других автопроизводителей выпускают значительно менее 100 тыс. автомобилей в год.
Средний объем производства одной модели в России значительно ниже уровня многих других стран. В США, Испании, Южной Корее и странах Восточной Европы он составляет около 119 тыс. автомобилей в год, в Китае и Бразилии - около 61 тыс., в России - лишь 27 тыс.
В сегменте автомобильных компонентов в России присутствуют также три основных типа производителей:
- российские производители в составе автомобильных компаний и самостоятельные предприятия (СОК, «Ителма» и др.). Они нацелены преимущественно на производство компонентов для существующих и устаревших российских моделей; располагают в основном морально и физически изношенной технологической базой; характеризуются нехваткой новых разработок и технологий, профессионального менеджмента; не имеют достаточных инвестиционных ресурсов и инжиниринговых навыков для освоения новых видов продукции и расширения клиентской базы; имеют низкий уровень качества, не позволяющий поставлять продукцию международным автоконцернам и производителям автокомпонентов;
- совместные предприятия российских и иностранных производителей (ZF, «Faurecia», «Delphi» и др.). Располагают относительно современными технологиями и оборудованием, полученными от международных партнеров; фокусируются на производстве технологически простых компонентов с низким уровнем добавленной стоимости (бамперы, жгуты, светотехника и т.д.), разработанных международными партнерами, или на лицензионной сборке сложных компонентов с низким уровнем локализации субкомпонентов (КПП, двигатели и пр.); практически не имеют прав на интеллектуальную собственность, собственного инжиниринга и НИОКР; имеют узкую специализацию ‒ обычно в небольшом ассортименте продуктов из одной-двух категорий компонентов;
- иностранные производители компонентов («Lear», «Bosch», «FederalMogul» и др.). Имеют низкий уровень локализации субкомпонентов и сырья, узкую специализацию и неразвитую клиентскую базу, что приводит к малым масштабам производства; ориентированы на поставки на внутренний российский рынок; фокусируются на технологически простых компонентах с низким уровнем добавленной стоимости (сиденья, свечи, выхлопные системы и т.п.).
Технический уровень создаваемой в последние годы российской автомобильной продукции в основном соответствует международным требованиям, правда, с существенной задержкой (до 4-7 лет) по времени их применения ‒ в частности, в отношении выбросов вредных веществ, обеспечения защиты пешеходов при дорожно-транспортных происшествиях, оснащения электронными системами обеспечения устойчивости и т.п. Имеется определенное отставание и по уровню надежности, ресурсу, топливной экономичности, уровню комфорта, по использованию в серийном производстве передовых технических идей и технологий.
Затраты на НИОКР у российских автопроизводителей не превышают 1% годовой выручки, а в ведущих зарубежных компаниях - не менее 4-5%. Это приводит к тому, что цикл развития новых моделей в России значительно длиннее, в результате модельный ряд обновляется заметно медленнее. Если за норму брать средний показатель затрат на НИОКР у глобальных производителей (4%), Россия должна направлять на эти цели не менее 44-53 млрд рублей в год.
Российские компании инвестировали в развитие отрасли в долевом отношении от объема реализации в 4-5 раз меньше своих иностранных конкурентов. Это является следствием недостаточной эффективности привлечения кредитов. Сегодня практически невозможно привлечь кредитные средства ни по срокам, сопоставимым со сроком окупаемости автомобильных производств (6-7 лет), ни по средним ставкам (8-10% годовых). А ведущие зарубежные автопроизводители привлекают долгосрочные средства по ставкам 5-6% и менее.
Повышение конкурентоспособности остается ключевым условиям роста экспорта. Россия все еще отстает от глобальных конкурентов по издержкам и качеству продукции. Можно выделить семь важнейших условий превращения российской автомобильной промышленности в отрасль, соответствующую международным стандартам:
- масштабный и стабильный внутренний спрос;
- конкурентные факторы производства и эффективная инфраструктура;
- предсказуемое и стимулирующее государственное регулирование;
- критическая масса локальных и локализованных производителей;
- эффективная сеть поставщиков комплектующих, включая базовые материалы;
- эффективный и гибкий производственный процесс по всей цепочке добавленной стоимости;
- ориентированные на потребителя продукты и продажи.
Масштабный и стабильный внутренний спрос
Восстановление спроса на автомобили после кризиса 2008‒2009 гг. оказалось в России более быстрым, чем обычно бывает после кризиса. Политика утилизации старых автомобилей, проводимая в 2011‒2012 гг., способствовала росту продаж на 600 тыс. машин. Важными факторами послужили также возвращение коммерческого кредитования покупок и восстановление уровня доходов населения.
Дальнейший рост спроса будет более медленным, однако достаточно стабильным, что обусловлено относительно низким уровнем автомобилизации в России (290 машин на тысячу жителей, в то время как в Восточной Европе ‒ 400, в Западной Европе ‒ 560 и в США ‒ 740). Кроме того, большая часть зарегистрированных автомобилей являются устаревшими по западным стандартам, что также должно способствовать дальнейшему росту спроса.
В то же время отрасль продолжает отличаться высокой волатильностью. Спрос коррелирует с макроэкономическими показателями, такими как рост реального дохода населения, цены на нефть, уровень процентных ставок и др. Колебания нефтяных цен могут вызывать квартальные скачки спроса на автомобили. Все это делает российский автомобильный рынок наиболее неустойчивым в мире среди стран-крупных автопроизводителей с уровнем отклонения в месячных продажах, в два раза превышающим уровень Бразилии, США, Германии и даже Китая.
В течение последних четырех лет в пиковые месяцы объем продаж автомобилей в России был в среднем в четыре раза выше по сравнению с кризисными месяцами. Такая волатильность угрожает развитию российской автомобильной промышленности. Это ведет к высокому дисконтированию рисков в процессе корпоративного планирования и снижению уровня инвестирования в проекты, что ставит под угрозу процесс модернизации, расширения производства и мощностей.
В этой связи от государства требуется выстраивание долгосрочных и эффективных стимулирующих мер и механизмов, чтобы противостоять резким колебаниям рынка, включая использование тарифных механизмов, стандартов безопасности и экологичности. Другой эффективной мерой борьбы с волатильностью рынка является стимулирование экспорта. Необходимо также иметь наготове меры на случай непредвиденных обстоятельств, связанных с кризисом или резким подъемом конъюнктуры. В периоды кризисов к таким мерам относятся программы утилизации, которые стимулируют покупателей заменять старые автомобили на новые; в периоды быстрого роста к экстренным мерам можно отнести ограничения потребительского кредитования.
Конкурентные факторы производства и эффективная инфраструктура
Быстро растущие издержки, возможно, представляют собой наибольшую угрозу развитию российской автомобильной промышленности. Переоцененный рубль, жесткий рынок труда и низкая производительность способствуют повышению издержек производства. В 2013 г. уровень заработной платы, скорректированный на уровень производительности труда, был в России в 7 раз выше, чем в 2000 г. Для сравнения, в Бразилии и Китае этот показатель вырос только в 2 раза. В других странах рост был еще более низким (рис. 2).
Рис. 2. Динамика трудовых издержек* в автомобильной промышленности России и ряде развивающихся стран (заработная плата, скорректированная на производительность труда), 2000 г. - 100**
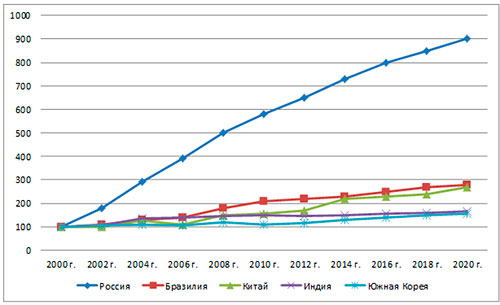
** В 2000 г. индекс трудовых издержек был равен 100.
Для того, чтобы выжить в острой конкурентной борьбе, российскому автопрому требуются коренные изменения. Этот тезис подтверждается статистическими и аналитическими исследованиями авторитетных организаций, таких как «Автостат». Существующее положение дел не устраивает ни потребителей, ни производителей. По данным ВЦИОМ, автолюбители ездят преимущественно на старых отечественных машинах (до 2006 года выпуска) по причине их доступности. Более современные модели для своего класса дороги, иностранные не доступны большинству граждан.
Старые автопредприятия испытывают нехватку в современных технологиях. Новым заводам не хватает ресурсов. Отдельные локализованные производства плотно сотрудничают с мировыми автомобильными брендами, что позволяет им создавать собственные перспективные разработки. Благодаря этому, возможность выпускать недорогую и надежную технику приобретает реальные очертания.
Перспективы развития отечественного автопрома
В конце 2015 года Минпром РФ по материалам исследования Boston Consulting Group (международная консалтинговая компания) разработал «Стратегию развития автомобильной промышленности на период до 2020 года». Программа предусматривает следующие шаги.
- Максимально полное насыщение отечественными машинами внутреннего рынка.
- Увеличение до максимума доли .
- Развитие популярных в РФ и за рубежом российских брендов.
- Производство ключевых комплектующих, локализация производства основной продукции и комплектации всех марок.
- Расширение патентной базы и НИОКР.
Разработчики «Стратегии» видят 4 возможных сценария развития автомобильной промышленности: текущий вектор, партнерство, закрытый рынок, крупный экспортер. Наиболее реальным представляется второй путь – «Партнерство». Именно этот сценарий взят за основу государственной политики, в рамках которой российский автопром должен получить около 600 млрд. руб. К сожалению, «тактических» мер эта стратегия не дает, однако ожидаемые результаты представляет.
- с 60% до 20% в денежном выражении.
- Производство отечественных транспортных средств составит 2,38% ВВП России.
- На каждую 1000 населения РФ российские легковые автомобили приобретут 363 человека.
- Количество ДТП снизится на 25-30%.
В документе приведены объемы инвестиций по годам в крупнейшие автозаводы: АвтоВАЗ, Газ, КАМАЗ, Sollers. С учетом низкой привлекательности российского автопрома для крупных инвесторов, сдвиги налицо. Соглашения о сотрудничестве подписаны у ВАЗа с Sollers и Renault, у КамАЗа с Daimler AG. В 2010 году открыт завод Peugeot- Citroen и Mitsubishi Motors в Калуге, Volkswagen запустил производство Skoda Fabia.
История развития российского автопрома
Начало истории автомобилестроения в Российской Империи относят к концу XIX века. Техническая новинка не получила признания в среде дворянства. Отечественные разработки почти прекратились, возобновившись лишь в 1917 на заводе по производству вагонов в Риге. Здесь собирали продукцию сначала на базе импортных комплектующих, а позже – собственного производства.
С началом Первой мировой войны, правительство финансировало деньги на строительство автопредприятий в Ярославле и Москве (АМО). На период войны рижский автомобильный завод перешел на выпуск самолетов и ракет. Его специализация была использована в СССР в космической отрасли. Первый советский легковой автомобиль выпущен на АМО в 1924 году. Модель Ф15 была далека от мировых образцов. Завод реконструировал и освоил на нем выпуск грузовиков корпорации США Ford Motor. В период 1931-33 годов он стал называться ЗИС. Дальнейшее развитие ЗИС получил во время Отечественной войны. Его вывезли на Урал, где образовались УльЗиС и УралЗиС.
По лицензии компании Ford Motor грузовые и легковые автомобили начали выпускать в Горьком (ныне Нижний Новгород). Завод ГАЗ демонстрировал большую производительность, его продукция шла на оснащение советской армии. Одновременно, во время войны велись конструкторские разработки легкового авто. Они завершились выпуском отличной, единственной в своем роде, Победы. Эта машина подняла репутацию автомобильной промышленности СССР. Интерес к ней оказался настолько высоким, что были созданы модели в экспортном исполнении. И продавались за рубежом – это был прорыв!
Последующие этапы развития автопрома СССР приходятся на середину прошлого века. Появились автомобильные заводы ВАЗ, ГАЗ, МАЗ, КрАЗ, КамАЗ, ЗИЛ, УАЗ. Из них сегодня на территории РФ работают предприятия на Волге (ВАЗ, КамАЗ, УАЗ), в Нижнем Новгороде (ГАЗ). Советские машины составляют две трети всех легковых автомобилей в стране. Это Волга, Ока, Нива, Москвич, Жигули, Запорожец. Грузовики марок КамАЗ, МАЗ, КрАЗ, ЗИЛ известны и пользуются заслуженной популярностью не только на внутреннем рынке, но и далеко за пределами России. Машины обладают неоспоримыми достоинствами:
- автомобили надежные и морозоустойчивые;
- техника обеспечена недорогим техническим обслуживанием и запчастями;
- высокая проходимость машин обусловлена условиями их эксплуатации на сложных дорогах России;
- низкая, по сравнению с зарубежными аналогами, стоимость автомобилей.
И еще. Несмотря на неказистый внешний вид, отечественные легковушки отличаются удивительной живучестью. Неутомимая «Победа», быстрая красавица «Волга», старые, надежные трудяги «Москвичи» и «Жигули». Значит, и российский автопром, который ассоциируется сейчас с низким качеством, мог достигать высоких успехов. Отрасль нуждалась в и . Вместо этого случился непоправимый провал 1990-2000 годов.
Современное состояние российского автомобилестроения
Из старых крупных автозаводов в РФ работают АвтоВАЗ, ГАЗ, КамАЗ. За последние 10 лет открылись совместные предприятия с различными иностранными компаниями.
Отставание автопрома России в производстве легкового транспорта компенсируется выпуском тяжелых автобусов и спецтехники.
Активно развивается АвтоВАЗ, совершенствуя свою Ладу. В 2015 открыт автосалон Lada в Венгрии. Выпускает автобусы Липецкий автомобильный завод. Заслуженные «Пазики» превратились в современные низкопольные автобусы марки ПАЗ. На выпуске сельхозтехники и больших автобусов специализируется ГолАЗ. Тяжелые «Уралы» продолжают сходить с конвейеров УралАЗ. Первая в РФ частная компания АК «ДЕРВЕЙС» появилась в 2002 году на Северном Кавказе.
Вид автотранспортного средства | Состояние отечественного производства | Сравнение по итогам 2013 года (данные OICA) |
Тяжелые автобусы | Первенство в Европе. | 173 148 единицы –
23 107 единицы – Россия 12 460 – Евросоюз |
Спецтехника, | Марка популярна в РФ и мире: грузовики, магистральные , военная техника. | Свои заводы размещены в Казахстане, Эфиопии, Пакистане, во Вьетнаме. Грузовик « » –неоднократный победитель «Дакара». |
Легковой сектор | В коммерческих и промышленных целях широко используются ГАЗель, Соболь, Садко, Волга. | |
Внедорожники | Полноприводные УАЗы активно трудятся в армии, подразделениях МЧС, МВД. |
Тенденции развития российского автомобильного производства
Рост выпуска отечественных начался с 2010 года, однако, незначительными темпами. Основным направлением развития принята стратегия производства у себя иностранных моделей. Появилась совместная разработка Chevrolet-Niva. Зарубежные концерны строят на территории РФ свои автозаводы. Примерами могут служить «Ford Motor Company», «Соллерс-Набережные Челны». Иностранные легковые транспортные средства марок BMW, Chevrolet, Hummer, Kia собирают на Автоторе в Калининградской области.
Наша продукция конкурентоспособна при . Экспорт ее стал возможен, и в этом направлении есть перспективы. Необходимо изучать и интенсивно занимать свободные крупные рынки. Поставки во Вьетнам, Иран, Алжир составят к 2020 году соответственно, 15, 30 и 22 тыс. единиц шасси и кузовов. Расширение экспорта может способствовать восстановлению и устойчивому развитию отечественного автопрома.
В рамках «Стратегии» планируется поднять занятость в отрасли с 0,8% до уровня передовых «автомобильных» стран. В ЕС она составляет в среднем 2%. Хорошие перспективы для автопрома видят специалисты в практике внедрения специальных инвестиционных контрактов. Шанс для развития отрасли в России дает также сокращение производства иномарок.
Сегодня сложно представить нашу жизнь без автомобиля. Они заполонили все дороги, ведь это не только эффективный способ быстро добраться из точки А в точку Б, но и отличная возможность перевозить грузы или большое количество пассажиров. Хотелось бы рассказать о том, чем примечателен Горьковский автомобильный завод, да и как вообще автопром развивался в России. Поверьте, тут есть о чём поговорить, ведь собственного производства на территории РФ появились достаточно давно.
Вступление
Отечественная история автомобилестроения началась еще в далёком 1896 году, когда люди увидели первый российский автомобиль. Он имел двигатель внутреннего сгорание, а его конструкторами принято считать Яковлева и Фрезе. В 1930-х годах в Нижнем Новгороде (сейчас город Горький) была основана компания НАЗ, которую позже переименовали в ГАЗ. На заводе выпускались как легковые, так и грузовые марки автомобиля по лицензии уже известной тогда компании Ford Motors. Именно Горьковский автомобильный завод в те времена стал основой строения транспортных средств. Уже к 1938 году СССР добилось больших успехов, так как ГАЗ, наряду с другими менее крупными предприятиями (ЯГАЗ, КИМ и т.п.) смог выйти на первое место по производству грузовиков во всей Европе. Еще до начала ВОВ государство выпустило более одного миллиона автомобилей, что было для того времени большой цифрой. Несомненно, начало войны очень затормозило развитие данной отрасли.
В 70-х годах наладился интенсивный выпуск армейских грузовиков и другой тяжёлой техники. Более 600 000 машин в год производил Волжский автомобильный завод, находящийся в Тольятти. Именно в эти времена появились так называемые «Жигули» и «Нивы» - полноприводные комфортабельные транспортные средства. Уже в 1976 году был возведён еще один передовой завод - «КамАЗ». В среднем за год там производилось 150 000 единиц грузовой техники и порядка 250 000 штук дизельных двигателей.
Как развивалось российское автомобилестроение?
Что же касается развития отрасли непосредственно в РФ, то в 1992 году начался кризис. Количество грузовой техники, выпускаемой заводами, сократилось в 5-6 раз, общественного транспорта стало меньше в 10 раз, а легковых авто с конвейеров сходило на 30% меньше. Но автомобилестроение в России постепенно выходило из плачевной ситуации. К примеру, ГАЗ и ВАЗ смогли выпустить даже несколько новых моделей, например, ВАЗ-2110, ГАЗ-3110 "Волга" и другие. Уже ближе к 2000-м годам появилась известная "Лада Калина" 2118, ГАЗ 31105 "Волга"/ГАЗ-2117 и другие модели. Тем не менее кризис не был преодолен полностью. По этой простой причине большая часть Российского автопрома пережила слияние, в результате которого образовались холдинги Группа ГАЗ (раньше "Руспромавто") и "Соллерс".
К 2002 году активно начинают производить иномарки. Примерно половина из всего того, что было выпущено (точнее, около 42%), были иностранные модели (легковые). Грузовой транспорт тоже занимал свою долю на рынке, приблизительно 8%, а автобусы - 10%. Благодаря тому, что количество иностранных компаний, отвечающих за производство и сборку транспорта на территории Российской Федерации, в 2009 году резко увеличилось, доля, отводимая на иномарки на отечественном рынке, стала больше. Очевидно, что основанные автомобильные альянсы благотворно влияют на развитие автомобилестроения. Это касается как продаж, так и популярности марки. Именно поэтому можно с уверенностью сказать, что автомобилестроение в России будет успешно развиваться и дальше при поддержке иностранных компаний.
История Горьковского автомобильного завода
Данное предприятие было основано В. И. Молотовым еще в 1932 году. На заводе выпускают легковую технику, а также микроавтобусы и лёгкие грузовики. Еще до 2005 года предприятие работало как «ОАО» Горьковский автомобильный завод, но в ходе масштабной реструктуризации было создано дочернее производство грузовой и легковой техники, которое стало носить название уже ООО «ГАЗ». Спустя 4 года, в 2009, произошло сокращение рабочего персонала, было уволено 2 000 сотрудников, осталось порядка 25 000 человек. В настоящее время Группа «ГАЗ» содержит в себе несколько дивизионов - «Автокомпоненты», «Лёгкие автомобили». В первый входит заготовочное производство, то есть всё то, что может быть продано. Оно хранится на складе. Как правило, это колёса, рулевые механизмы, кузова автомобилей и многое другое. Что касается второго дивизиона, то это мощности автомобилестроительного предприятия «ГАЗ» по выпуску легковой техники.
Первое, что выпустили с конвейера данного завода еще в 1932 году - это грузовой автомобиль НАЗ-АА (ГАЗ-АА) (1,5 тонны). В том же году конструкторы начали разрабатывать седан НАЗ-А, имеющий пятиместный кузов. Уже к 1933 году Горьковский автомобильный завод выпустил автобус марки ГАЗ-03-30. Количество сидячих мест составляло 17 штук. В 1934 был собран 2-х тонный грузовик ГАЗ-ААА, и в это же время - К 1938 году с конвейера сошёл ГАЗ-ММ - грузовой автомобиль, который мог похвастаться пятьюдесятью «лошадьми» под капотом. В это же время был сконструирован и запущен в эксплуатацию санитарный транспорт ГАЗ-55, а также ГАЗ-60 с увеличенной проходимостью за счёт использования гусеницы.
Развитие в 1941-1945 годы
Во время боевых действий «ГАЗ» был полностью реконструирован под производство военной техники. В первое время выпускали легковой военный автомобиль марки ГАЗ-64, а уже к октябрю был сконструирован знаменитый лёгкий танк Т-60. Его конструкция не единожды усовершенствовалась с целью увеличения эксплуатационных характеристик, что позволяло получить преимущества в бою. Считалось, что во время войны данный завод был одним из самых мощных с точки зрения производительности, поэтому тут модифицировалось большое количество техники, кроме того, и броня Т-60. Спустя пару месяцев был сооружен Т-70, который вскоре стал одним из самых используемых в Красной армии. Если говорить о том, какие в годы войны были центры автомобилестроения, то два из крупнейших - это «ГАЗ» и московский завод №37. Тут постоянно выпускалась лёгкая техника, например, БА-64Б, БА-64, а также легковая машина повышенной проходимости ГАЗ-67.
Наиболее успешной работой инженеров завода был танк Т-80, основное преимущество которого заключалось в двухместной башне. Таким образом, был устранен недостаток Т-70, который имел всего одно место. Тут же было налажено производство СУ-12 - самоходной артиллерийской установки. Не будет лишним отметить, что конструкторы машиностроительного завода постоянно разрабатывали бронированную и гусеничную технику, которая по множеству причин так и не вошла в эксплуатацию. За время войны фашистская Германия бомбила «ГАЗ» около 7 раз. В целом было разрушено более 50 зданий с оборудованием. Более 30 000 человек трудились над восстановлением технологической цепочки, что удалось всего за 100 дней. После победы завод был награждён Ленина и почётной медалью Великой Отечественной войны первой степени.
Развитие в послевоенные годы (1946-1960)
Сказать, что сразу по окончании войны началась замена оборудования, - ничего не сказать. Практически всё, что было использовано до войны, утилизировали и тут же открыли производство новых моделей автомобилей. Например, в 1946 вышел грузовик ГАЗ-51 и легковой автомобиль «Победа» М-20. Нельзя не отметить выпуск снегоболотохода ГАЗ-47, который передвигался на гусеницах и обладал большой проходимостью. Примерно к 1949 году конструкторы разработали первый прототип Джипа - ГАЗ-69, который имел большой успех. Следом за ним был создан седан «ЗИМ». Он был представительского класса, поэтому позволить себе такой транспорт могли лишь единицы. Активно выпускались грузовые авто ГАЗ-52,53, завоевавшие в 1952 году в Брюсселе Гран-при и множество других наград. Эта же награда была присвоена ГАЗ-21 и «Волге» ГАЗ-13.
В течение 1953 года активно разрабатывался комфортабельный внедорожник. В качестве прототипа использовался сам автомобиль имел название М-72. В 56-м году «Победу» сменил ГАЗ-21, который стал очень популярным у населения, так как это была удобная, мощная и надёжная машина. Наряду с этим производились грузовики третьего поколения, такие как ГАЗ-56, который мог перевозить до 1,5 тонн. Самым мощным был ГАЗ-53 - до 3,5 тонн. Было достаточно много техники, которая так и не сошла с конвейера по множеству причин. Виной этого были разного рода дефекты, а также уязвимые места моделей. Те же ГАЗ-52,53 выпускались в течение 4-х лет и пережили достаточно много модификаций.
Что выпускалось в 1961-1991 годах?
К 1960 году полностью закончилось обновление военной линейки автомобилей. На конвейере были ГАЗ-52, ГАЗ-53 и ГАЗ-66. На последние два автомобиля впервые начали устанавливать новые силовые агрегаты, например, карбюраторный двигатель V8, который отличался высокой мощностью. Уже в 70-е годы в производство массово было запущено авто ГАЗ-24 «Волга», которая пришла на замену 21-й модели. В 77-м году вышла с конвейера знаменитая «Чайка» ГАЗ-14. Данный седан отличался не только высокой надёжностью, но и достаточным уровнем комфорта, а также высокими эксплуатационными характеристиками. К 1973 было создано ПО «ГАЗ», которое включило в себя 11 заводов-филиалов. Примерно к концу 70-х годов начинается существенная модернизация «Волги», а также разрабатывается следующее поколение грузовых авто.
В 81-м году с конвейера «ГАЗ» сошла десятимиллионная машина. Благодаря высокой квалификации сотрудников удалось разработать двигатель с воздушным охлаждением (дизель), который был применён на грузовике ГАЗ-4301. Руководство в 1980-х годах приняло ответственное решение переходить на дизельное производство. Исходя из этого, нужно было провести массовую реконструкцию. Первые моторы сошли с конвейера в 1993 году. Безусловно, в течение нескольких лет можно было заметить застой, который характеризовался малыми выпусками. Например, рестайлинговая модель «Волги» ГАЗ-3102 выпускалась в количестве нескольких тысяч в год. Впервые для нужд малого бизнеса конструкторы работали над грузовиком массой 3,5 тонн. Горьковский автомобильный завод использовал систему конструирования САПР, а также ускоренные испытания выпущенного транспорта, что позволяло достаточно быстро производить новые модели.
История завода в 1992-2000 года
Сразу после распада Советского Союза начался глубокий кризис. Сложно сказать, как развивалось российское автомобилестроение в это время, но одно известно точно: Горьковский завод одним из первых приспособился к новым рыночным условиям, что позволило ему удержаться на плаву. Выпускались автомобили с использованием оригинальных дизельных двигателей с воздушным охлаждением. Это были модели ГАЗ-3306, 3309 и 4301. Но без государственной поддержки такой транспорт практически не имел спроса, что сулило большие убытки. Однако в это же время удалось немного увеличить продажи «Волги», примерно в 2 раза. Конструкторы создали первый пикап - «Волга» ГАЗ-2304», который именовали «Бурлаком». Но не весь транспорт завода имел успех, например, седан бизнес-класса 3105 практически не покупали из-за его необоснованно высокой цены. Отчасти это было обусловлено тем, что транспорт иностранного производство внедрялся всё глубже и создавал конкуренцию отечественным автомобилям.
В 94-м году появилась знаменитая «Газель». Полная масса данного автомобиля составляла 3,5 тонны. Нельзя не отметить, что именно эта модель была одной из наиболее популярных за все время работы предприятия. Она активно использовалась для нужд малого и среднего бизнеса, а также для других целей. Многие эксперты считают, что именно «Газель» спасла предприятие от банкротства и позволила обеспечить ему устойчивое положение на рынке. Так как автомобилестроение в России не стояло на месте, и было достаточно много конкурентов, нужно было создать нечто такое, что смогло бы поднять экономику завода. Это было маршрутное такси ГАЗ-32213 «Газель». В декабре 95-го года Горьковский автомобильный завод выпустил свой пятнадцатимиллионный автомобиль.
Примечательные события 2000-2010 года
Стоит заметить, что в 2000 году пакет акций завода был куплен крупной компанией под названием «Базовый элемент». Был создан холдинг «РусПромАвто», а далее «Группа ГАЗ». На сегодняшний день завод занимает одно из лидирующих мест по производству легковых автомобилей на территории России. Реорганизация, проведенная в 2001 году, позволила наладить выпуск модельного ряда пикапов и внедорожников «Атаман». Но из-за недостаточного финансирования большинство проектов так и не воплотили в жизнь. Финансовая ревизия позволила выйти на рентабельный уровень (впервые за десятилетие). Большое внимание руководство уделяло лёгкому транспорту массой до 3,5 тонн. К 2005 году значительно вырос спрос на грузовики ГАЗ-3307, 3309. Чтобы сократить отставание от ведущих мировых производителей, был использован опыт этих же компаний.
Было принято решение расширить сферы бизнеса, то есть продавать ГАЗ не только на территории РФ и близлежащих государств, но и в пределах дальнего зарубежья. Это позволило бы заводу стать одним из крупнейших игроков на мировом рынке автопрома. Конструкторы создавали автобусы и газели из запчастей, которые поступали из Англии (SKD). Но из-за банкротства была свёрнута компания LDV, поставки были прекращены, и воплотить проект в жизнь не удалось. В целом, 2010 год выдался вполне успешным по сравнению с предыдущим. Было выпущено на 78% больше легковых автомобилей (70 300 штук) и на 61% - грузовых. Экспорт осуществлялся более чем в 30 стран мира.
Экономический кризис
В 2008 году настал глубокий кризис. Буквально через несколько месяцев возникли проблемы со сбытом товара. Площадки были полностью загружены, именно по этой простой причине несколько раз останавливался конвейер. Спросом не пользовался даже «ГАЗ» самосвал, дизель на котором был не только качественный, но и относительно экономный. Из-за кризиса принимались вынужденные меры, например, было уволено около 10 000 человек. В 2009 году планировали воплотить в жизнь долгожданный проект по производству Volga Siber. Но как оказалось на практике, он был неудачным. С конвейера сошло всего 1718 седанов, а реализовано было меньше половины - 418 штук. Также из-за кризиса в 2009 году был продан завод в Британии, где выпускались автомобили марки Maxus. Постепенно модель была выведена и из российского рынка. Чтобы хоть как-то увеличить количество продаж, цена на разработанную «Газель» была сброшена до 6 000 долларов. Но и это не помогло, удалось продать всего 600 машин.
После этого попытки выйти из кризиса не закончились, и впервые начался серийный выпуск машин марки «Газель-Бизнес». Авто имело ряд модификаций и относительно доступную цену, что немного привлекло покупателей. Были предприняты и другие меры, благодаря которым удалось хоть немного выровнять экономическую ситуацию - это был большой шаг, который сделал Горьковский автомобильный завод. «ГАЗ» выпустил дизельную модификацию автомобиль «Газель-Бизнес». И уже в 2010 году конструкторы приступили к проектированию 4-х тонного грузовика с двигателем объёмом 3,8 литра. В конце декабря было подписано соглашение с Daimler о выпуске на мощностях «ГАЗ».
Заключение
Как вы видите, история Горьковского автомобильного завода довольно обширная и увлекательная, и на этом она не заканчивается. Дело в том, что в настоящее время «Группа ГАЗ» остается самым крупным производителем грузовых автомобилей, автокомпонентов, а также спецтехники на территории Российский Федерации. Что касается последних изменений, то это подписание соглашения в 2011 году с концерном GM о производстве Chevrolet Aveo на мощностях «ГАЗ». Летом был подписан еще один контракт длительностью на 8 лет - Volkswagen Group и «ГАЗ» заключили сделку на производство 110 000 машин в год. Уже в 2013 году в серийное производство выпущена «Газель Next». Изначально планируется спускать с конвейера порядка 50 единиц транспорта в сутки, а дальше увеличить это количество втрое и наладить экспорт в Турцию, Польшу и другие страны. Экономическая ситуация сейчас достаточно стабильная, и все конвейера работают, поэтому продажи обещают быть активными. Как уже было отмечено выше, история автомобилестроения на этом совсем не заканчивается. Будем надеяться, что отечественные производители порадуют нас новыми удивительными машинами.
Похожие статьи